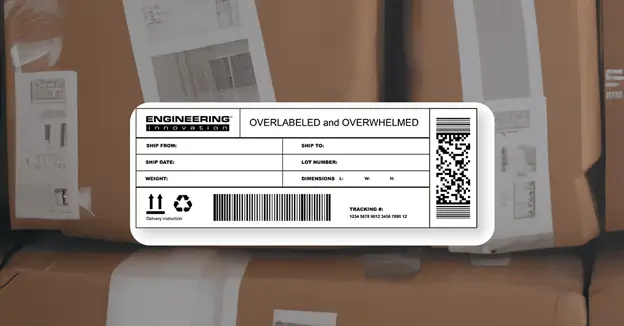
When too much information is a bad thing, what should shippers do?
The shipping and distribution industry is like a big puzzle where things are constantly moving, covering logistics, transportation, and supply chain management.
Many people cooperate to ensure products seamlessly travel from the maker to their final stop without any issues.
Getting packages to customers quickly is crucial for distributors to keep them happy.
To succeed, the industry must maintain smooth processes that avoid delays, mistakes, or extra costs.
Efficient Labeling Matters
Good labeling is really important in shipping and distribution.
Labels are like messages between the people sending, carrying, and getting packages. They tell important things about what’s inside, where it’s going, and how to handle it.
Putting the right labels on packages quickly and correctly helps sort and send them where they need to go, making everything work better in the shipping and distribution process.
What is “Overlabeling”?
While labeling holds importance, the industry faces an issue known as “overlabeling.”
This occurs when parcels get too many labels, leading to numerous problems.
It results in higher costs and has negative effects on the environment.
Overlabeling presents a significant challenge in shipping and distribution. In the next sections, we will discuss why it happens, its consequences, and how we can address it.
Understanding Overlabeling
In parcel shipping, overlabeling happens when there are too many labels on packages, more than needed for good communication in the supply chain.
This can cause problems because extra or unnecessary labels make the distribution process more complicatedIn parcel shipping, overlabeling happens when there are too many labels on packages, more than needed for good communication in the supply chain.
Consequently, this can cause problems because extra or unnecessary labels make the distribution process more complicated.
Common Causes of Overlabeling
Several factors add to the prevalence of overlabeling in the shipping industry:
1. Lack of Standardized Guidelines: Absence of universally accepted guidelines for labeling practices can result in inconsistencies and an inclination toward overlabeling.
2. Manual Handling Errors: Human errors in the labeling process, such as misinterpretation of requirements or unintentional duplication, can lead to overlabeling.
3. Stringent Regulations: Excessive regulatory requirements or varying standards across regions may prompt distributors to add extra labels to ensure compliance, even when not strictly necessary.
4. Legacy Systems and Processes: Outdated labeling systems or practices that haven’t evolved with technological advancements may contribute to inefficiencies and overlabeling.
Examples of Overlabeling Scenarios
To show how overlabeling directly affects things, let’s look at examples like redundant information labels. In this case, parcels end up with duplicate labels saying the same thing, causing confusion and possible delays in processing.
Additionally, some companies use too many compliance labels, adding multiple labels to meet different regulations. This makes things unnecessarily complicated and increases costs.
Another issue happens when labels saying “fragile” or “handle with care” are put on items that don’t really need special treatment. This results in extra work without any real benefit.
Understanding these reasons and examples is vital for creating effective plans to reduce overlabeling and make the shipping and distribution processes work better.
Negative Effects on Distributors
Increased Costs
Additional Expenses Associated with Excess Labels:
- Overlabeling leads to a direct increase in operational costs as distributors incur expenses related to the production, procurement, and application of unnecessary labels.
- Budgets allocated for labeling materials may be stretched beyond necessity, impacting the financial bottom line.
Impact on Packaging Materials and Resources:
- The surplus application of labels contributes to a higher consumption of packaging materials, including adhesives and paper.
- Distributors may find themselves managing excess inventory of labeling materials, tying up capital that could be used more efficiently.
Operational Inefficiencies
1. Delays in Processing and Sorting Due to Excessive Labels:
- The presence of numerous labels on parcels can lead to delays in processing as sorting systems may struggle to interpret and prioritize relevant information.
- Sorting facilities may experience bottlenecks, slowing down the entire distribution chain.
2. Potential Errors in Package Handling and Routing:
- Overlabeling increases the likelihood of errors in package handling, as redundant or conflicting information may confuse workers or automated systems.
- Misrouted packages, delayed deliveries, and increased instances of lost items can result from these operational inefficiencies.
Environmental Impact
1. Excess Waste from Unnecessary Labels:
- Overlabeling contributes directly to increased waste generation in the form of redundant labels that serve no functional purpose.
- Disposal of excess labels adds to environmental concerns, especially in regions where waste management infrastructure is not optimized.
2. Sustainability Concerns in the Shipping Industry:
- The environmental impact of overlabeling extends to broader sustainability issues within the shipping industry.
- Distributors may face scrutiny from environmentally conscious consumers and regulatory bodies, potentially impacting their brand reputation and market standing.
Understanding these negative effects on distributors highlights the urgency for industry stakeholders to address the overlabeling issue and implement measures to enhance operational efficiency, reduce costs, and contribute to sustainable practices in the shipping and distribution sector.
Emphasizing the Importance of Accurate Labeling
In the dynamic landscape of shipping and distribution, accurate labeling stands as a cornerstone for operational excellence.
Industry leaders are implementing robust strategies to ensure precision in labeling practices, recognizing the pivotal role it plays in streamlining operations and minimizing costs.
To fortify the foundation of accurate labeling, comprehensive educational initiatives are being embraced.
Specialized training programs are empowering industry professionals with insights into the significance of precision.
By emphasizing the role of accurate labeling in streamlining operations, these programs contribute to a more informed workforce.
Transparent communication channels within the supply chain are paramount to accurate labeling.
Establishing clear guidelines and ensuring that all stakeholders are well-informed about labeling requirements and best practices are crucial steps.
This proactive approach reduces the likelihood of overlabeling, stemming from uncertainties in the labeling process.
Integrating robust quality control measures into the labeling process is a proactive strategy.
This involves implementing checks and audits to identify and rectify errors before parcels enter the distribution network.
By prioritizing quality control, industry players mitigate the risks associated with overlabeling, ensuring accuracy from the outset.
Implementing Technology Solutions for Automated Labeling
In an era driven by technological innovation, the shipping and distribution sector is leveraging cutting-edge solutions for automated labeling, aiming for a seamless and error-free operational landscape.
Optimized Automated Labeling Systems:
Investing in automated labeling systems is a strategic move to optimize accuracy and efficiency.
This helps in reducing the risk of overlabeling associated with outdated or suboptimal technology (and manual error).
Industry leaders recognize the importance of staying at the forefront of automation for enhanced operational outcomes.
Data Integration and Validation:
Ensuring smooth integration of labeling systems with other supply chain technologies is paramount.
This facilitates real-time data validation, minimizing discrepancies that might prompt overlabeling.
The cohesive integration of technologies ensures a synchronized and accurate labeling process.
Adaptive AI and Machine Learning:
The integration of adaptive artificial intelligence (AI) and machine learning algorithms is transforming the intelligence of labeling systems.
These technologies allow systems to adapt to changing scenarios, minimizing errors over time.
The industry is witnessing the power of AI in enhancing the efficiency and accuracy of automated labeling processes.
Encouraging Industry Collaboration for Standardization
Recognizing the need for a standardized approach, industry leaders are championing collaborative efforts to establish guidelines, share best practices, and address challenges associated with overlabeling.
Establishing Industry Guidelines:
Collaboration with industry associations and regulatory bodies is instrumental in developing and promoting standardized labeling guidelines.
This collaborative approach reduces confusion and ensures a universal adoption of best practices, minimizing the risks of overlabeling.
Call to Action for Industry Stakeholders to Address the Issue
It is imperative for industry stakeholders, including distributors, manufacturers, and technology providers, to proactively address this issue.
Collaboration and a commitment to adopting efficient labeling practices are essential components of any comprehensive strategy.
As the industry looks toward the future, embracing emerging technologies, participating in responsible labeling initiatives, and staying informed about potential regulatory changes will be crucial.
By adopting efficient labeling practices, the shipping and distribution sector can not only mitigate the negative effects of overlabeling but also contribute to a more sustainable, cost-effective, and streamlined supply chain.
Summary
In conclusion, overlabeling poses significant challenges to the shipping and distribution industry, leading to increased costs, operational inefficiencies, and environmental concerns.
The negative impacts extend beyond financial considerations to include delays, errors, and sustainability issues.